Can Tungsten Carbide Rust Over Time?
When it comes to durable and long-lasting materials, tungsten carbide often stands out as a top choice. Known for its exceptional hardness and resistance to wear, this compound is widely used in everything from industrial tools to jewelry. But a common question that arises among users and enthusiasts alike is: will tungsten carbide rust? Understanding the nature of this material and its interaction with the environment is key to appreciating its true resilience.
Tungsten carbide’s reputation for toughness is well-earned, but many wonder how it holds up against corrosion, especially rust—a common issue for many metals. While rust typically refers to the oxidation of iron and steel, the behavior of tungsten carbide in similar conditions can be less straightforward. Exploring its chemical properties and how it responds to moisture and air can shed light on why it is often considered a reliable choice for harsh environments.
This article will delve into the fundamentals of tungsten carbide’s composition and clarify whether it is susceptible to rust or other forms of corrosion. By gaining insight into these aspects, readers will be better equipped to care for tungsten carbide products and understand their longevity in everyday use.
Corrosion Resistance Properties of Tungsten Carbide
Tungsten carbide is renowned for its exceptional hardness and wear resistance, but its behavior in terms of corrosion and rust is equally significant, especially in environments prone to moisture and oxidation. Unlike iron or steel, tungsten carbide itself is a compound formed by tungsten and carbon, which inherently lacks the iron content necessary for traditional rust formation (iron oxide). Therefore, pure tungsten carbide does not rust in the conventional sense.
However, the corrosion resistance of tungsten carbide depends heavily on the binder material used in its composite form. Most tungsten carbide products are not 100% tungsten carbide but consist of tungsten carbide particles bonded together with a metal binder, typically cobalt. The cobalt binder is susceptible to corrosion and oxidation, which can lead to surface degradation and a phenomenon sometimes mistaken for rust.
Key factors influencing corrosion in tungsten carbide tools and components include:
- Binder Composition: Cobalt binders can corrode when exposed to acidic or alkaline environments, leading to surface pitting and loss of material integrity.
- Environmental Exposure: High humidity, saltwater, and corrosive chemicals accelerate binder corrosion.
- Surface Finish and Coatings: Polished surfaces and protective coatings like titanium nitride (TiN) can significantly reduce corrosion risk.
- pH Levels: Acidic or basic conditions increase the likelihood of binder corrosion.
This corrosion primarily affects the binder phase, causing the surface to roughen and potentially exposing more tungsten carbide particles to the environment, which can accelerate wear.
Comparison of Tungsten Carbide and Steel Corrosion Behavior
To better understand how tungsten carbide compares to steel regarding rust and corrosion, the following table highlights their respective properties and susceptibilities:
Property | Tungsten Carbide (WC-Co Composite) | Steel (Carbon or Stainless) |
---|---|---|
Rust Formation | Does not rust; binder (cobalt) may corrode | Prone to rust (iron oxide) unless stainless or coated |
Corrosion Resistance | High hardness, moderate corrosion resistance; binder vulnerable | Variable; stainless steel resists corrosion well, carbon steel less so |
Effect of Moisture | Minimal effect on carbide; binder may corrode with prolonged exposure | Significant rusting risk with moisture and oxygen |
Effect of Chemicals | Vulnerable to acids and alkalis affecting binder phase | Varies widely; some steels are highly resistant, others corrode easily |
Protective Coatings | Commonly coated (TiN, TiAlN) to protect binder and improve wear | Often painted, plated, or stainless to prevent rust |
Best Practices to Prevent Corrosion of Tungsten Carbide
While tungsten carbide is resistant to rust, proper handling and maintenance are essential to extend the life of tungsten carbide tools and parts, especially those containing cobalt binders. Recommended practices include:
- Keep Dry: Store tools in dry environments to minimize moisture exposure.
- Use Protective Coatings: Applying coatings such as TiN or other nitrides can create a barrier against corrosive elements.
- Avoid Harsh Chemicals: Prevent exposure to acids, bases, and chlorides that can attack the binder.
- Clean After Use: Remove residues, especially from metalworking fluids or salts, which can be corrosive.
- Inspect Regularly: Check for signs of binder corrosion or surface pitting and address issues promptly.
- Consider Binder-Free Alternatives: For extreme corrosion environments, explore tungsten carbide composites with alternative binders like nickel or use fully sintered carbide with minimal binder.
Corrosion Testing Methods for Tungsten Carbide Materials
To evaluate the corrosion resistance of tungsten carbide materials, several standardized testing methods are employed in industrial and research settings. These tests help determine the susceptibility of the binder phase and the overall composite to different corrosive environments:
- Salt Spray Test (ASTM B117): Simulates a saline fog environment to evaluate surface corrosion and pitting over time.
- Potentiodynamic Polarization: Measures the corrosion rate and behavior in specific chemical solutions.
- Immersion Testing: Prolonged exposure to acidic or alkaline solutions to observe material degradation.
- Electrochemical Impedance Spectroscopy (EIS): Assesses the protective properties of coatings and the corrosion resistance of the substrate.
- Microstructural Analysis: Using SEM or EDS to detect corrosion initiation points and binder degradation.
These tests enable manufacturers and users to select appropriate materials and coatings tailored to their operational environments.
Summary of Corrosion Characteristics
- Tungsten carbide itself does not rust due to the absence of iron.
- The cobalt binder in tungsten carbide composites is vulnerable to corrosion, which can degrade tool performance.
- Environmental factors such as moisture, chemicals, and pH strongly influence corrosion risk.
- Protective coatings and proper maintenance significantly extend the lifespan of tungsten carbide tools.
- Testing and material selection are critical for applications involving corrosive environments.
Understanding these nuances ensures that tungsten carbide components are used and maintained effectively, minimizing corrosion-related failures.
Corrosion Resistance of Tungsten Carbide
Tungsten carbide is a composite material consisting primarily of tungsten and carbon atoms bonded together in a crystalline structure. Unlike pure metals, it does not exhibit typical metallic corrosion mechanisms such as rusting. Rust is specifically the oxidation of iron or its alloys, resulting in iron oxide formation. Since tungsten carbide contains no iron, it cannot rust in the traditional sense.
However, corrosion and surface degradation are still relevant concerns in certain environments. The corrosion resistance of tungsten carbide depends on several factors:
- Composition: The ratio of tungsten to carbon and the presence of binders such as cobalt influence corrosion behavior.
- Environmental conditions: Exposure to acids, alkaline solutions, or oxidizing agents can affect the surface integrity.
- Surface finish: Polished or coated tungsten carbide surfaces resist corrosion better than rough or porous ones.
Material | Rust Formation | Corrosion Susceptibility | Common Corrosion Products |
---|---|---|---|
Pure Iron/Steel | Yes | High (in moist, oxygen-rich environments) | Iron oxides (rust) |
Tungsten Carbide | No | Low to Moderate (depending on environment) | Tungsten oxides, cobalt corrosion products (if binder present) |
Pure Tungsten | No | Low (forms stable oxide layer) | Tungsten oxides |
Factors Influencing Corrosion of Tungsten Carbide Components
Although tungsten carbide itself is highly corrosion-resistant, many commercial tungsten carbide tools and components are produced as composites with metallic binders, typically cobalt. These binders can be susceptible to corrosion, impacting the overall durability of the part.
Key factors affecting corrosion include:
- Cobalt binder content: Higher cobalt percentages increase susceptibility to chemical attack, especially in acidic or chloride-rich environments.
- Environmental exposure: Acidic solutions, saltwater, and oxidizing agents accelerate binder corrosion and may cause pitting or surface degradation.
- Surface treatments: Coatings such as TiN (titanium nitride) or surface polishing reduce binder exposure and enhance corrosion resistance.
- Temperature and humidity: Elevated temperature and moisture increase corrosion rates of binders.
Preventing Corrosion and Maintaining Tungsten Carbide Integrity
To ensure longevity and maintain the performance of tungsten carbide tools and parts, consider the following protective measures:
- Proper material selection: Use tungsten carbide grades with lower binder content or alternative binders like nickel or ruthenium for improved corrosion resistance.
- Surface coatings: Apply hard coatings (TiN, TiAlN, DLC) to act as barriers against corrosive environments and reduce binder exposure.
- Cleaning and maintenance: Regular cleaning to remove corrosive agents such as salts or acids helps prevent binder degradation.
- Storage conditions: Store in dry, controlled environments to minimize moisture-induced corrosion.
- Avoid harsh chemicals: Limit exposure to strong acids or bases that can attack the cobalt binder.
Common Misconceptions About Tungsten Carbide and Rust
There are several misconceptions regarding tungsten carbide and its susceptibility to rust:
- “Tungsten carbide rusts like steel”: This is inaccurate since tungsten carbide contains no iron and cannot form iron oxide rust.
- “Tungsten carbide is completely corrosion-proof”: While highly resistant, the cobalt binder phase can corrode under certain conditions.
- “Surface discoloration is rust”: Oxidation of tungsten or binder corrosion may cause discoloration but is chemically distinct from rust.
Summary of Tungsten Carbide Corrosion Characteristics
Property | Description | Impact on Performance |
---|---|---|
Rust Formation | Does not rust; no iron oxide formation | Maintains structural integrity without typical rust degradation |
Binder Corrosion | Cobalt binder can corrode in harsh environments | May lead to surface pitting, reduced hardness, and tool failure |
Oxidation | Tungsten forms stable oxides on the surface | Generally protective, but excessive oxidation can affect appearance |
Environmental Resistance | High resistance to moisture and mild chemicals | Suitable for most industrial applications with proper care |
Expert Insights on the Corrosion Resistance of Tungsten Carbide
Dr. Emily Chen (Materials Scientist, Advanced Composites Lab). Tungsten carbide is renowned for its exceptional hardness and wear resistance, but when it comes to rusting, it is important to clarify that tungsten carbide itself does not rust. Rust is a form of iron oxide that forms on iron or steel when exposed to moisture and oxygen. Since tungsten carbide is a compound of tungsten and carbon, it does not contain iron and therefore cannot rust in the traditional sense. However, the metal binder phase, often cobalt, used in tungsten carbide composites can corrode under certain conditions, so proper care and coatings are recommended to prevent surface degradation.
Mark Johansson (Corrosion Engineer, Industrial Coatings Inc.). From a corrosion engineering perspective, tungsten carbide tools and parts are highly resistant to oxidation and chemical attack, which makes them ideal for harsh environments. The primary concern is the binder material, typically cobalt, which can oxidize and degrade if exposed to moisture or acidic conditions. This degradation can lead to surface pitting or a loss of mechanical integrity over time. Therefore, while tungsten carbide itself does not rust, the composite material may require protective treatments to ensure longevity in corrosive environments.
Prof. Linda Martinez (Metallurgy Professor, National Institute of Materials Science). Tungsten carbide’s corrosion resistance is superior compared to many metals, but it is not completely impervious to chemical reactions. Rust specifically refers to iron oxide formation, which does not occur with tungsten carbide. However, depending on the manufacturing process and the binder phase used, some tungsten carbide alloys can experience surface oxidation or binder leaching under extreme environmental conditions. Proper maintenance and storage are essential to preserve the integrity of tungsten carbide components, especially in wet or chemically aggressive settings.
Frequently Asked Questions (FAQs)
Will tungsten carbide rust?
Tungsten carbide does not rust because it contains no iron, which is the primary metal that oxidizes to form rust.
Can tungsten carbide corrode under any circumstances?
While tungsten carbide is highly resistant to corrosion, it can degrade if exposed to strong acids or alkalis over extended periods.
How does tungsten carbide resist oxidation?
Tungsten carbide forms a stable, hard surface that resists oxidation, unlike ferrous metals that oxidize easily.
Is tungsten carbide suitable for use in humid or wet environments?
Yes, tungsten carbide is well-suited for humid and wet environments due to its excellent corrosion resistance and lack of rust formation.
Does the binder metal in tungsten carbide affect its corrosion resistance?
Yes, the cobalt or nickel binder in tungsten carbide can be susceptible to corrosion, which may affect the overall durability if exposed to harsh chemicals.
How should tungsten carbide be maintained to prevent surface degradation?
Regular cleaning with mild detergents and avoiding exposure to aggressive chemicals will help maintain tungsten carbide’s surface integrity.
tungsten carbide is highly resistant to rust and corrosion due to its unique chemical composition and structure. Unlike iron or steel, tungsten carbide does not contain significant amounts of iron, which is the primary element that oxidizes to form rust. This inherent property makes tungsten carbide an excellent choice for applications requiring durability and resistance to environmental degradation.
However, while tungsten carbide itself does not rust, it is often bonded with a metal binder such as cobalt, which can be susceptible to corrosion under certain conditions. Proper care and maintenance, including avoiding prolonged exposure to moisture and corrosive substances, are essential to preserve the integrity of tungsten carbide tools and components. Protective coatings and appropriate storage further enhance their longevity.
Overall, the exceptional hardness, wear resistance, and corrosion resistance of tungsten carbide make it a preferred material in various industrial and commercial applications. Understanding its properties and limitations ensures optimal performance and durability, minimizing concerns related to rust and corrosion in most practical uses.
Author Profile
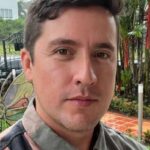
-
I’m Leroy Ambrose. I started with Celtic rings. Not mass-produced molds, but hand-carved pieces built to last. Over time, I began noticing something strange people cared more about how metal looked than what it was. Reactions, durability, even symbolism these were afterthoughts. And I couldn’t let that go.
This site was built for the curious, the allergic, the cautious, and the fascinated. You’ll find stories here, sure, but also science. You’ll see comparisons, not endorsements. Because I’ve worked with nearly every common metal in the craft, I know what to recommend and what to avoid.
So if you curious about metal join us at Walker Metal Smith.