Will JB Weld Effectively Stick to Aluminum Surfaces?
When it comes to repairing or bonding metal surfaces, choosing the right adhesive can make all the difference between a lasting fix and a temporary patch. Among the many options available, J-B Weld has earned a reputation for its strong, durable bonding capabilities. But how well does this popular epoxy perform when it comes to aluminum, a metal known for its unique properties and challenges? Understanding whether J-B Weld will stick to aluminum is essential for anyone looking to tackle metal repairs with confidence and precision.
Aluminum’s lightweight nature and resistance to corrosion make it a common material in automotive, household, and industrial applications. However, these same qualities can sometimes make it tricky to bond effectively. Adhesives must be able to adhere firmly without compromising the metal’s integrity or performance. J-B Weld, celebrated for its versatility and toughness, is often the go-to choice for metal repairs, but its compatibility with aluminum raises important questions about preparation, application, and long-term durability.
Exploring the interaction between J-B Weld and aluminum opens the door to understanding not only the adhesive’s strengths but also the best practices for achieving a secure bond. Whether you’re a DIY enthusiast, a professional mechanic, or simply curious about metal repair solutions, gaining insight into this topic will equip you with the knowledge to make informed decisions and
Adhesion Properties of JB Weld on Aluminum
JB Weld is a popular two-part epoxy adhesive known for its strong bonding capabilities on various surfaces, including metals. When applied to aluminum, JB Weld creates a durable chemical bond that can withstand significant stress, heat, and exposure to chemicals. The adhesive works by curing into a hard, rock-solid substance, filling gaps and adhering tightly to the metal surface.
The effectiveness of JB Weld on aluminum depends on several factors:
- Surface Preparation: Properly cleaning and roughening the aluminum surface enhances adhesion. Removing oils, dirt, oxidation, and other contaminants ensures maximum contact.
- Mixing Ratio: Accurate mixing of the resin and hardener components is critical to achieve optimal curing and bonding strength.
- Curing Time and Conditions: JB Weld typically requires 4–6 hours to set and 15–24 hours to fully cure at room temperature. Elevated temperatures can accelerate this process.
- Application Thickness: Applying the epoxy evenly and avoiding excessive thickness helps prevent weak spots and improves durability.
Surface Preparation Techniques for Aluminum
Achieving a strong bond with JB Weld on aluminum starts with meticulous surface preparation. Aluminum naturally forms an oxide layer that can interfere with adhesion if not treated correctly. The following steps are recommended:
- Cleaning: Use a degreaser or isopropyl alcohol to remove oils, grease, and dirt.
- Sanding: Abrade the surface with medium to fine-grit sandpaper (around 150–220 grit) to create a rough texture for mechanical bonding.
- Degreasing Again: After sanding, clean the surface once more to remove dust and residual oils.
- Drying: Ensure the surface is completely dry before applying JB Weld.
This process maximizes the epoxy’s ability to penetrate microscopic crevices and form a strong mechanical and chemical bond with the aluminum.
Performance Characteristics of JB Weld on Aluminum
JB Weld’s performance on aluminum is characterized by its high strength, temperature resistance, and durability. Below is a comparison of key properties relevant to bonding aluminum:
Property | JB Weld on Aluminum | Typical Aluminum Alloy |
---|---|---|
Tensile Strength | Approximately 3,960 PSI | Varies by alloy; typically 13,000–83,000 PSI |
Operating Temperature | Up to 550°F (288°C) | Melting point around 1,220°F (660°C) |
Cure Time | 4-6 hours to set; 15-24 hours full cure | Not applicable |
Water Resistance | Excellent once cured | Excellent |
Though JB Weld does not match the inherent tensile strength of aluminum alloys, its bond strength is sufficient for many repair and bonding applications, especially where welding or mechanical fastening is impractical.
Applications and Limitations
JB Weld’s ability to adhere to aluminum makes it ideal for a variety of repair tasks, including:
- Filling cracks or holes in aluminum surfaces
- Bonding aluminum parts where welding is not feasible
- Repairing aluminum tanks, pipes, or automotive components
- Sealing leaks in aluminum radiators or housings
However, users should be aware of certain limitations:
- JB Weld is not a substitute for welding in structural or load-bearing aluminum joints requiring maximum strength.
- The bond may degrade under continuous exposure to extreme mechanical stress or flexing.
- Curing times can be extended in cold or humid environments, affecting bond quality.
- Surface contamination or improper preparation can significantly reduce adhesion.
Best Practices for Using JB Weld on Aluminum
To maximize the performance of JB Weld on aluminum surfaces, consider the following best practices:
- Follow Manufacturer Instructions: Adhere strictly to mixing ratios and curing times.
- Ensure Proper Surface Preparation: Clean, sand, and dry the aluminum thoroughly.
- Apply Evenly: Use enough epoxy to fill gaps but avoid excess thickness.
- Clamp or Secure Parts: Maintain pressure during curing to improve bonding.
- Allow Full Cure: Avoid stressing the bond before the recommended curing time has elapsed.
- Use Appropriate Variants: JB Weld offers different formulations (e.g., high-heat, marine) tailored for specific conditions.
By following these guidelines, JB Weld can form a reliable, lasting bond on aluminum suitable for many maintenance and repair scenarios.
Adhesion Properties of J-B Weld on Aluminum Surfaces
J-B Weld is a widely recognized two-part epoxy adhesive known for its strength and versatility. When it comes to bonding aluminum, several factors influence the effectiveness of J-B Weld, including surface preparation, application method, and environmental conditions.
J-B Weld can adhere to aluminum surfaces effectively due to the following characteristics:
- Chemical Composition: J-B Weld’s epoxy resin and hardener create a strong cross-linked polymer that bonds well to metal substrates, including aluminum.
- Mechanical Bonding: Proper surface preparation enhances adhesion by increasing surface roughness, allowing the epoxy to anchor mechanically.
- Thermal Resistance: The cured epoxy withstands temperature variations typical in metal repairs, maintaining bond integrity.
However, aluminum’s natural oxide layer can inhibit adhesion if not properly addressed. Therefore, surface treatment is critical.
Surface Preparation for Optimal Bonding
Proper surface preparation is essential to maximize the bond strength of J-B Weld on aluminum. The following steps are recommended:
Step | Description | Purpose |
---|---|---|
Cleaning | Remove oils, grease, dirt, and oxidation using solvents such as isopropyl alcohol or acetone. | Ensures the surface is free from contaminants that reduce adhesion. |
Abrading | Use sandpaper (80-120 grit) or a wire brush to roughen the aluminum surface. | Increases surface area for mechanical bonding and disrupts the oxide layer. |
Degreasing | Wipe the abraded surface again with a solvent to remove residual dust and oils. | Prevents interference from contaminants during curing. |
Drying | Allow the surface to dry completely before applying epoxy. | Moisture can compromise the epoxy’s curing process and bond strength. |
Following these preparation steps can significantly improve the adhesion and durability of the J-B Weld bond on aluminum parts.
Application Tips for Using J-B Weld on Aluminum
To achieve the best results when bonding aluminum with J-B Weld, consider the following expert application guidelines:
- Mixing Ratio: Accurately mix equal parts of resin and hardener to ensure proper curing and maximum bond strength.
- Application Thickness: Apply the mixed epoxy in a consistent layer, typically 1/8 inch thick, to avoid weak points or insufficient bonding.
- Clamping: Apply moderate pressure or clamp the parts together to eliminate air pockets and ensure intimate contact.
- Curing Conditions: Allow the epoxy to cure at room temperature for at least 4-6 hours, with full strength achieved after 15-24 hours.
- Post-Cure Heating (Optional): Gentle heating (up to 150°F/65°C) can accelerate curing and improve bond strength but should be done cautiously to avoid aluminum distortion.
Performance Considerations and Limitations
While J-B Weld adheres well to aluminum when properly prepared and applied, certain limitations should be noted:
Factor | Impact on Bond Performance |
---|---|
Oxide Layer | Natural aluminum oxide can weaken adhesion if not removed or abraded. |
Exposure to Chemicals | Harsh solvents or acids may degrade the epoxy over time. |
High Stress or Load | J-B Weld provides good tensile strength but may not be suitable for high-impact or load-bearing structural repairs. |
Thermal Cycling | Repeated heating and cooling cycles can cause bond fatigue if not properly cured. |
It is advisable to evaluate the specific application requirements and consider mechanical fastening in combination with epoxy bonding for critical aluminum repairs.
Expert Evaluations on JB Weld’s Adhesion to Aluminum
Dr. Helen Martinez (Materials Scientist, Advanced Composites Lab). JB Weld exhibits strong adhesion properties on aluminum surfaces due to its epoxy resin base, which chemically bonds well with the metal’s oxide layer. Proper surface preparation, such as cleaning and roughening the aluminum, significantly enhances the bond strength and durability.
James Whitaker (Mechanical Engineer, Industrial Repair Solutions). In my experience, JB Weld can reliably stick to aluminum for a variety of repair applications, including structural fixes and sealing. However, the longevity of the bond depends on environmental factors like temperature fluctuations and exposure to moisture, so it’s critical to follow the manufacturer’s curing recommendations carefully.
Lisa Chen (Corrosion Specialist, Metalworks Consulting). JB Weld forms a robust adhesive layer on aluminum, but the key to success lies in meticulous surface preparation. Removing any oils, oxidation, or contaminants ensures optimal adhesion. When applied correctly, JB Weld provides a resilient and corrosion-resistant bond suitable for both indoor and outdoor aluminum repairs.
Frequently Asked Questions (FAQs)
Will JB Weld stick to aluminum effectively?
Yes, JB Weld is designed to bond strongly with aluminum surfaces, providing a durable and reliable repair when applied correctly.
How should aluminum be prepared before applying JB Weld?
Clean the aluminum thoroughly to remove grease, dirt, and oxidation. Lightly sanding the surface improves adhesion by creating a rough texture for the epoxy to grip.
Can JB Weld withstand high temperatures on aluminum parts?
Standard JB Weld can handle temperatures up to 500°F (260°C), making it suitable for many aluminum repairs exposed to moderate heat.
Is JB Weld waterproof when used on aluminum?
Yes, once fully cured, JB Weld forms a waterproof bond that resists moisture and many chemicals on aluminum surfaces.
How long does JB Weld take to cure on aluminum?
Initial set time is about 4-6 hours, with full curing achieved in 15-24 hours depending on temperature and humidity conditions.
Can JB Weld be used for structural repairs on aluminum?
JB Weld provides strong bonding for many applications but may not replace welding or mechanical fasteners for critical structural repairs on aluminum.
J-B Weld is a widely recognized epoxy adhesive known for its strong bonding capabilities on various materials, including metals. When it comes to aluminum, J-B Weld can effectively adhere to the surface, provided that proper surface preparation is undertaken. Cleaning the aluminum thoroughly to remove any oils, dirt, or oxidation is essential to ensure optimal adhesion and a durable bond.
The adhesive forms a robust, heat-resistant bond that can withstand mechanical stress and environmental factors, making it suitable for repairs involving aluminum parts. However, it is important to note that the strength of the bond depends on factors such as curing time, application thickness, and the condition of the aluminum surface. Following the manufacturer’s instructions carefully will maximize the performance of J-B Weld on aluminum.
In summary, J-B Weld is a reliable solution for bonding aluminum when applied correctly. Its versatility and durability make it an excellent choice for both temporary fixes and permanent repairs. Users should prioritize surface preparation and curing protocols to achieve the best results when working with aluminum substrates.
Author Profile
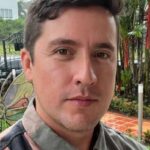
-
I’m Emory Walker. I started with Celtic rings. Not mass-produced molds, but hand-carved pieces built to last. Over time, I began noticing something strange people cared more about how metal looked than what it was. Reactions, durability, even symbolism these were afterthoughts. And I couldn’t let that go.
This site was built for the curious, the allergic, the cautious, and the fascinated. You’ll find stories here, sure, but also science. You’ll see comparisons, not endorsements. Because I’ve worked with nearly every common metal in the craft, I know what to recommend and what to avoid.
So if you curious about metal join us at Walker Metal Smith.